29/06/15 20:46 Filed in:
Concrete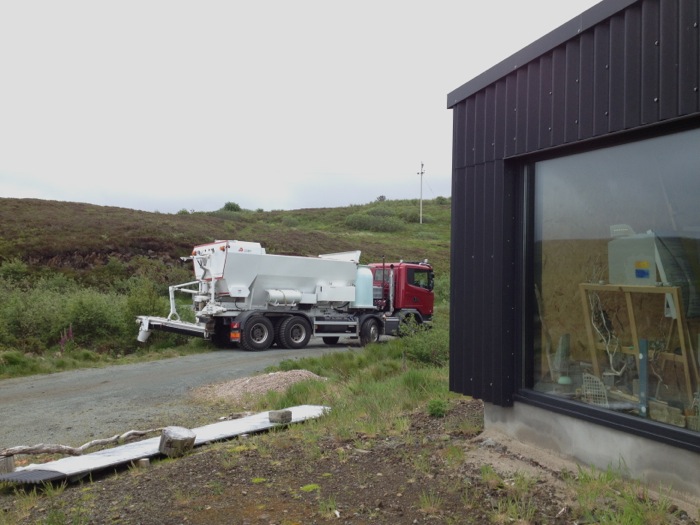
There is a great lorry on Skye, recently upgraded, that mixes the concrete on the lorry to a fairly exact mix so that you only use what you need with no wastage. The cost was just shy of £120 per cubic meter of concrete. The cost is also determined by the strength of the mix. We were told in the specification that we had to use a C25 strength. We decided on a stronger C30 mix that put up the cost to nearly £120 per m3.
The Lorry at over 40 tons was too heavy to use the track to get onto the site right next to the building. Sean therefore had got his dumper truck on site together with his digger which was ready on the Studio site. So the lorry poured the concrete into the dumper which then travelled over to the site where Sean used the bucket of his digger to very carefully place the initial 100mm of concrete into the trenches. Simon and I were in the trenches spreading the concrete with rakes so that it was level across the trench. We knew it was level as we had drilled vertical steel bar into the rock where the centre of each pier was. These were painted with yellow on their tips and they were level with each other across the trench. They were drilled to a height where just their tips would be showing when 200mm of concrete, at the shallowest point, had been poured. At 100mm from the top we placed the steel mesh carefully within each trench before filling up to the tip of each bar.
This work happened quickly and I am always amazed at how delicately Sean could use the digger and bucket to gently drop the concrete where we needed it. When we put the first steel mesh in we also placed each of the central pier cages over the middle of each of the vertical bars, already in position. Simon together with Sean built up the column around each of the piers so that there was a level area large enough for the blockwork to sit upon. This work was complete within a couple of hours. We used 6.3 m3 of C30 concrete. This was probably two or three cubic meters of concrete more if the ground had easily allowed us to dig 12 separate holes rather than four trenches with three piers in each trench.
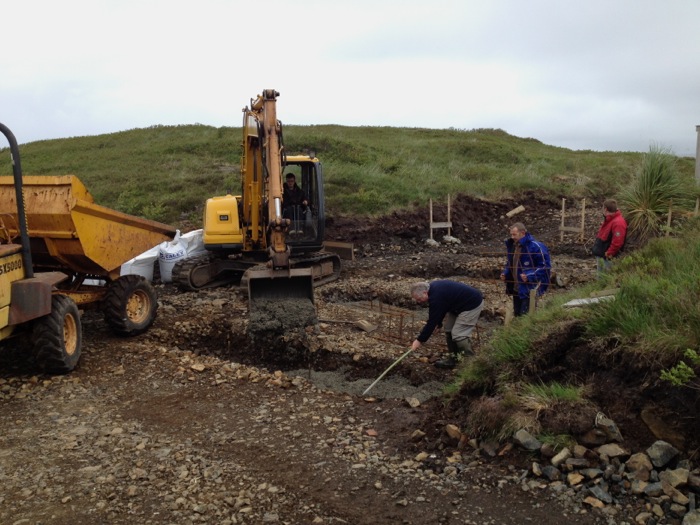
We left the concrete to set and would begin the following day on building the smallest piers. Before leaving we distributed the blocks and stacked them around the site so they were ready to hand at each place a pier was to be built. To have mixed all this on site would have taken days of hard work. So in two hours and thanks to a good access track the pour for the main foundations was done in around two hours.
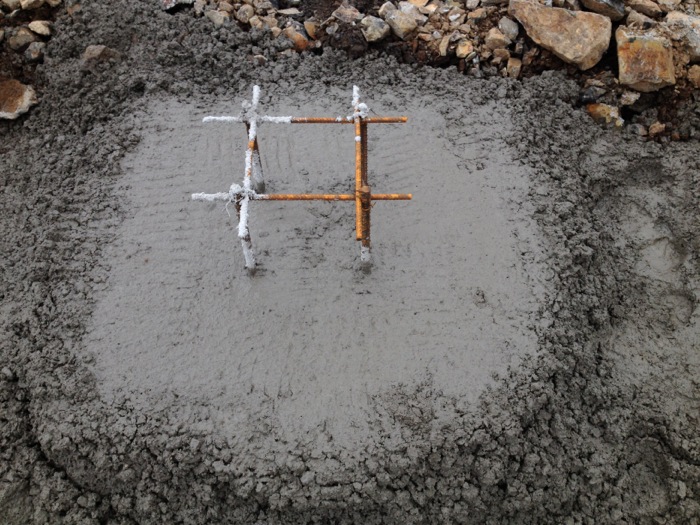
Tags: Footings
15/06/15 20:30 Filed in:
Final Floor Level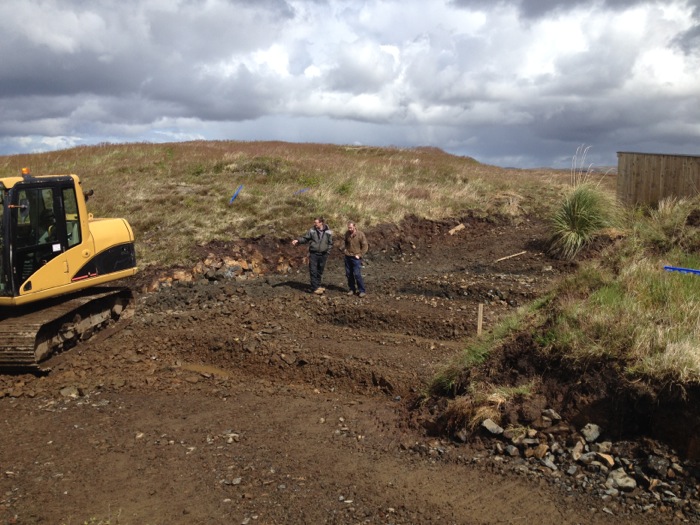
Once the trenches were dug, after we measured and marked the ground with yellow spray marker paint, we had to establish the level for each pier in each of the trenches.
The final floor level of the new studio was 3m lower than the final floor level of the Blackhouse some 70m away. There was a surveyors datum stake left from the build which marked the final floor level of the Blackhouse about 15m in front of the Blackhouse.
Simon had a fairly basic laser level and we took the level from this datum stake and marked the final floor level using the bleeps of the laser to tell us when we were at floor level of the Blackhouse close to the site of the new build. Once we had established this level we subtracted 3m to establish the final floor level of the studio.
We then set up a series of level boards on site with the final floor level marked on each, both length ways across the site of the building and width ways. By then using the level in combination with string lines we carefully established the position and level of each pier. The piers at the east end of the site were the shortest and those to the west of the site, front sloping end of the building, would be the highest. The building of piers allows you to deal with the discrepancies of height across the site by adjusting height of each pier.
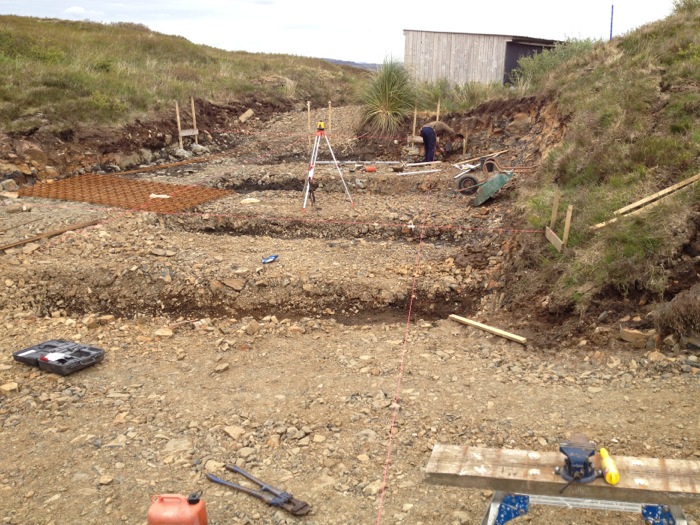
Once marked out we then had to cut the initial steel mesh for each trench which would be placed in the middle of the first foundation pour, minimum 200mm concrete mix, for each trench. As well as this mesh in each trench a further reinforced cage had to be made to sit on this mesh and be the central reinforced core of each pier. All of the steel needed to be prepared before the initial pour. This work with steel requires a metal cutter, angle grinder, and we also needed considerable heat to get the 16mm steel bar hot enough to bend at 90 degrees without tearing the steel. Simon made a bench with vice installed that would allow us to lever the bar in order to bend it. We used a blow torch running off a propane bottle. This gave us just enough heat.
This work took three days ready for the concrete to arrive on site.
Tags: Levels
06/06/15 18:30 Filed in:
Groundworks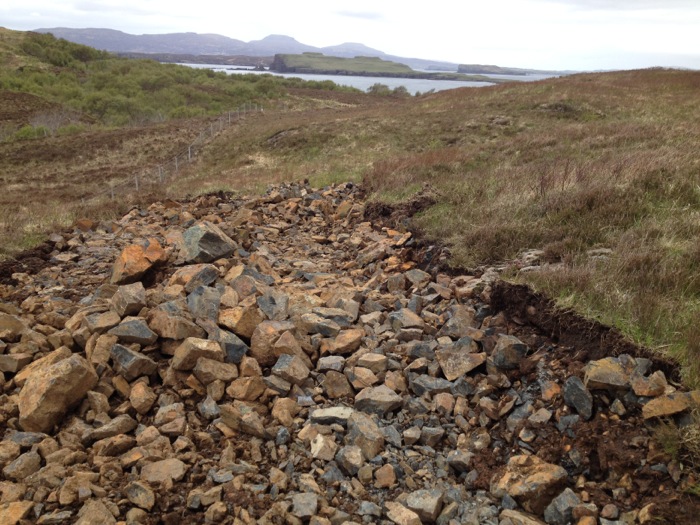
It took Sean about five days in total to establish a smooth track and also to scrape back the house site to the rock below the peat. This involved a day or so of rock breaking with a large hydraulic pick on the end of the 15 ton digger. The hire of Sean and the digger cost £30 an hour and £40 an hour when breaking rock. In establishing the track Sean had carefully removed the top 600mm or so of peat, complete with plants, bog myrtle, small rowan bushes and placed these carefully by the side of the track. Treating the ground in this way allows the peat and plants to survive intact.
He said we could then decide if we then want to place it back to make a smaller track to the completed house. He said he had learnt this technique while working on the large wind farms on Skye, where the contractors were strict about restricting damage to the soil and fauna. He assured us that it really works as a technique. Indeed all of the grass and shrubs are still thriving.
The rock that was broken was used to smooth and grade the track down to the house site. On the fourth day, Simon who is working with me, marked out the position of the trenches, holes for the piers upon which the building would stand. They were initially separate holes to bedrock for each pier but as Sean was excavating he found a small band of clay that needed to be dug out which then made us decide that four trenches across the width of the build would allow us a better way of setting the foundations.
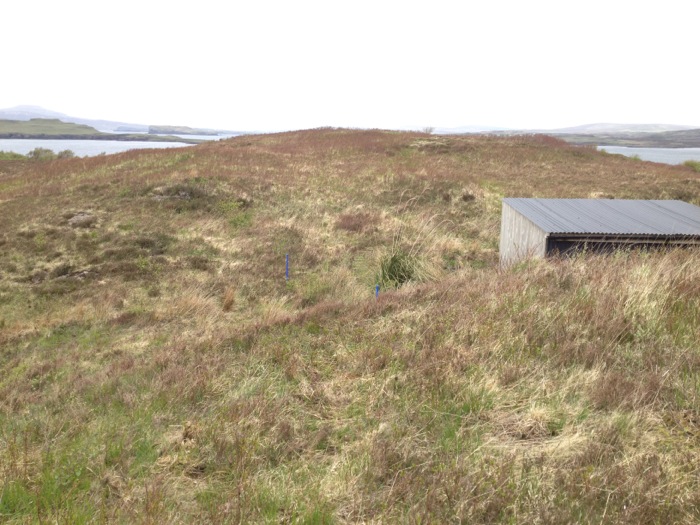
Despite a survey before and a structural engineer on site this small band of clay hadn't been discovered. The trenches were deeper where the clay band had been found, this would require more concrete to get the level that we needed for all of the piers. The ground work is where costs can be unpredictable as you never completely know what you will find until the digger digs. This was not a big problem but required a solution that became four trenches with three piers across in each trench, The solution had the building on bedrock, but we would need more concrete to establish the level across the trenches. This probably increased costs at the concrete stage by £300.
Tags: Digging, Rock Breaking