30/07/15 14:32 Filed in:
Floor The floor was built off of two parallel wooden beams or rails. They were made up of six engineered wooden beams each 3.5m long and notched at their joints to overlap and be bolted onto the steel brackets and to each other.
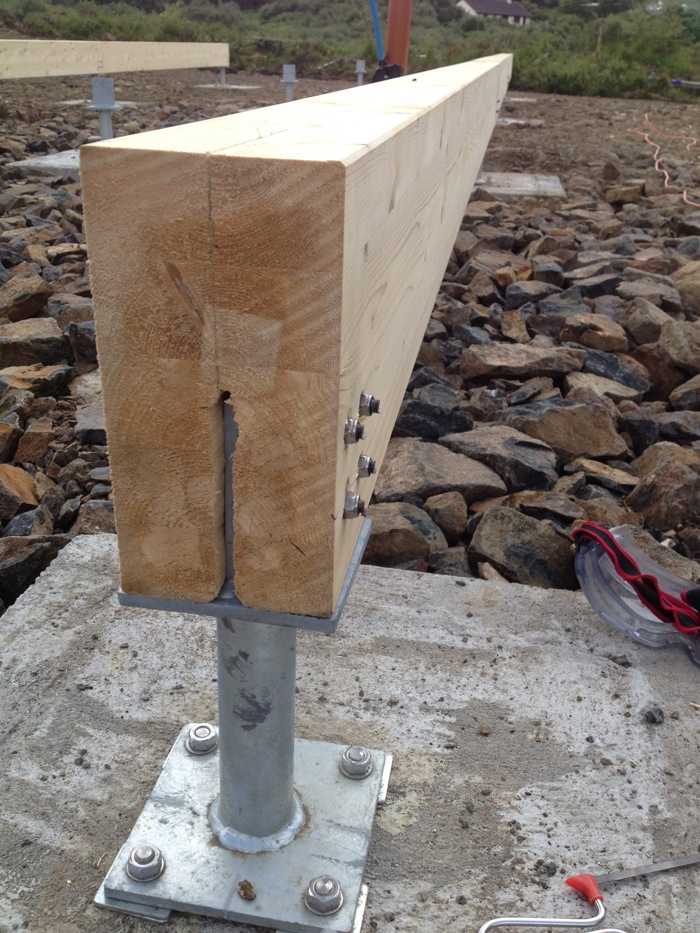
The engineers in developing their calculations asked us to add the middle set of piers to support the middle of the floor and anchor it in these points as well. Originally the drawings had shown eight piers on the external perimeter of the walls. This requirement for the extra four middle piers added considerable cost to the build and seems like massive overkill even given the extreme wind loadings on Skye.
The joists for the floor then spanned the two rails and were attached at each end by joist hangers. We also decided to add a central set of support nogins or dawns as they are called in Scotland to add extra rigidity to the floor. This was advised by the joiner who has a great deal of experience in building with wood.
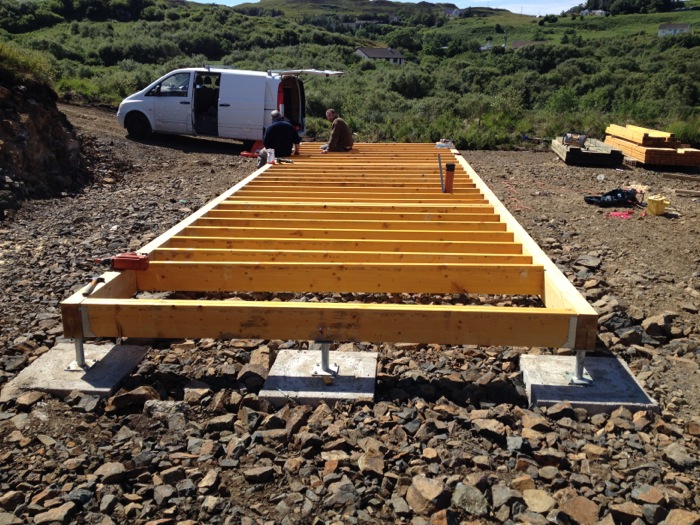
Certainly the floor feels incredibly strong and anchored to the foundations. Before starting on these builds I did a week long wooden building course at the Centre for Alternative Technology (CAT) in Wales. This was really useful in giving me the basic principles based on
Walter Segal's methods of wooden construction. Certainly the houses we stayed in at CAT were much lighter in construction than our builds on Skye. Recently
Piers Taylor shared a link to the
Segal method in a short online documentary, worth a look.The studio build at Fiscavaig shares many of the techniques of Segal's method. On this build the frame is all wooden built off of a set of piers and within the structture of the build itself there will be no wet trades, tools are simple, saws, bolts, nails, string lines and levels.
Tags: Floor
23/07/15 14:14 Filed in:
Wood Structure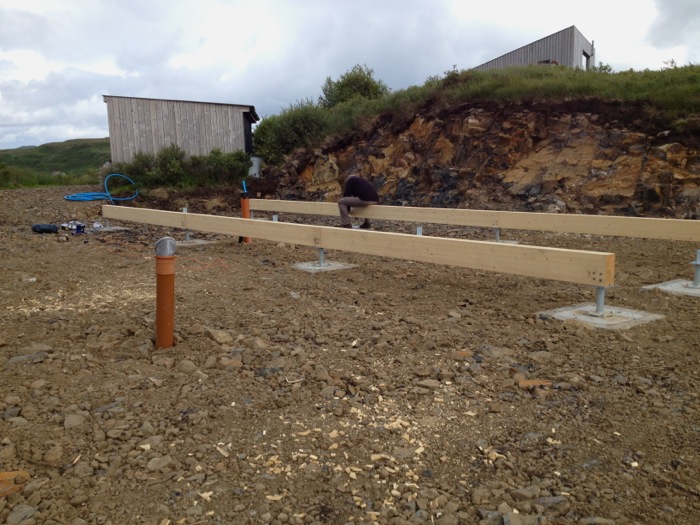
We could now start on the wooden structure. Once you have been involved in a few builds, and this is the one I have been most involved with in terms of physical labour, you begin to understand the rhythm and pacing of the build process.
The groundworks, preparation, concrete foundations, blockwork, measuring, checking levels and final floor height, seem to go quite slowly and all of the work is then covered over to provide a relatively flat working area on site. This work, with a few gaps waiting for the concrete lorry to get to us between its other jobs, waiting for weather etc seems to go very slowly. But the careful preparation of all of these elements set the scene for the rest of the build going smoothly.
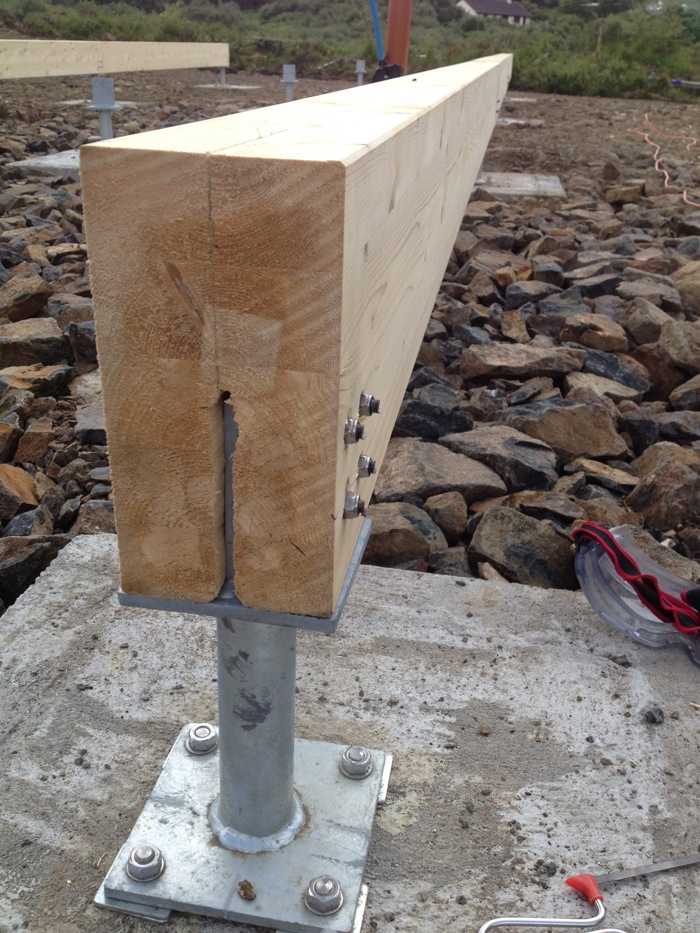
Without this careful prep, making sure of measurement of piers, checking final floor levels, making sure materials can get on to the site the rest of the build without this would become much more time consuming, difficult and energy sapping. This is an important thing to consider as the build for the Studio is only being done, usually by just two of us on site. We have had Sean with his digger doing the groundworks and Bekah is coming for ten days to help with the wooden frames. Most of the time it is Simon, the joiner, and me the labourer. It would be easy if things weren't prepared carefully to become disenchanted with the build and for it to slow up and fall behind. In Skye because of the often extreme winds in winter it is really important that outside work is completed between the spring and Autumn Equinox.
If all is prepared then the construction of the wooden floor, wall frames, roof, sheathing is relatively quick and can give you a false impression that the build is nearing completion. Once this big, impressive work is done, the internal work slows down again. Working on your own seems to magnify the task in front of you. It is great to work as a pair or group as you tend to keep each others spirits up and can sort out problems between you rather than feeling left alone with, what can feel like and enormous task. It also helps working with a very experienced joiner like Simon who is looking far ahead of myself for possible problems in the next stages of the build. Nothing can trump knowledge based on sound experience.
Tags: Wood, Joinery
15/07/15 14:02 Filed in:
Costs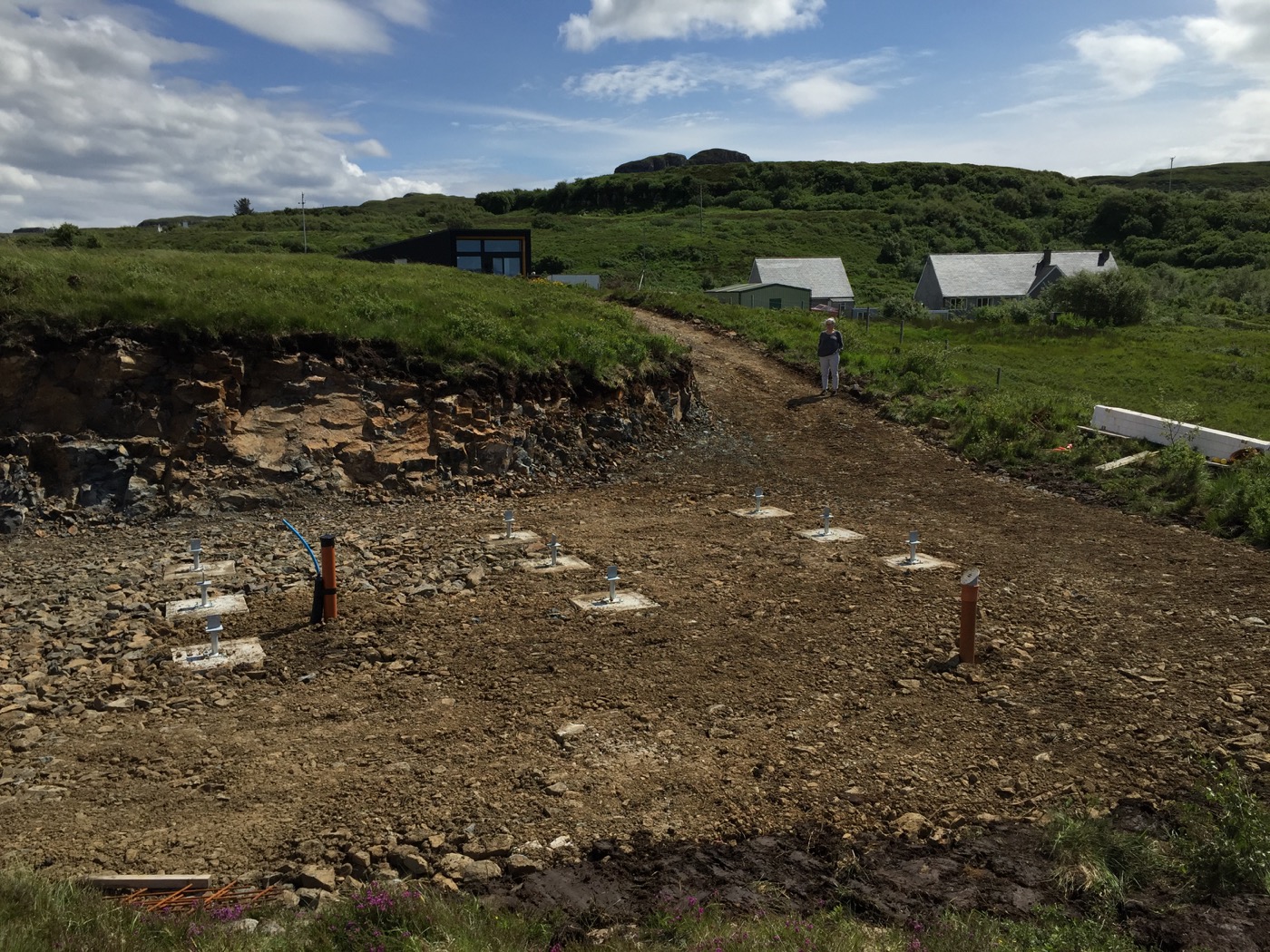
So up to this point the costs had been. I will quote the prices without Vat as if you are building a residence you can claim Vat back on materials.
Groundworks:The construction of 90m track into the site. Scraping back to rock on the house site, Breaking rock for track and house site. Digging trenches for foundations. Transporting concrete from Lorry to site and filling trenches.
Return to site for infill, soak away construction, grading of site and end of road.
£4680.00
Materials:Concrete ready mixed on site 6.3m3 £743.00
Ballast, steel, Blocks, cement £690.00
Steel Galvanised Brackets to hold Wooden floor beams £1100.00
Labour £1500
Total to get out of the ground £8713Tags: Costs
13/07/15 13:52 Filed in:
Infill | groundworks | PopUpsSean came back on site with his digger for two days to infill around the piers. This required taking the rock face back by 1.5m breaking the rock up as infill between the piers in order to make the site level for the rest of the build.
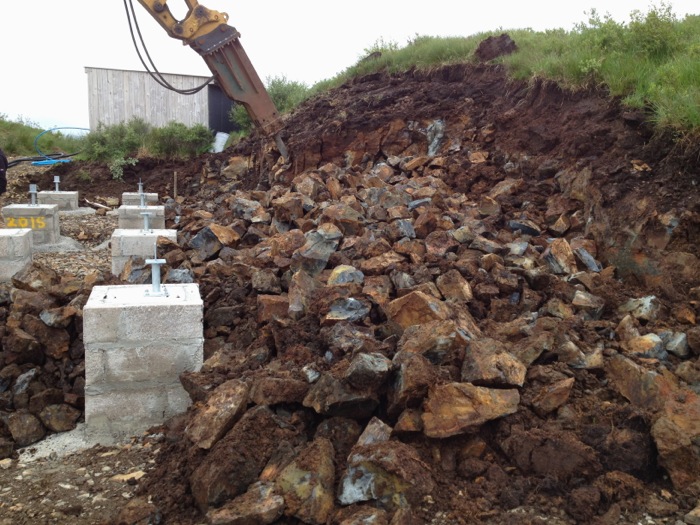
Luckily we also had some rock left over form the excavations for the Blackhouse so Sean used this to complete the infill and grade the track more gently into the site.
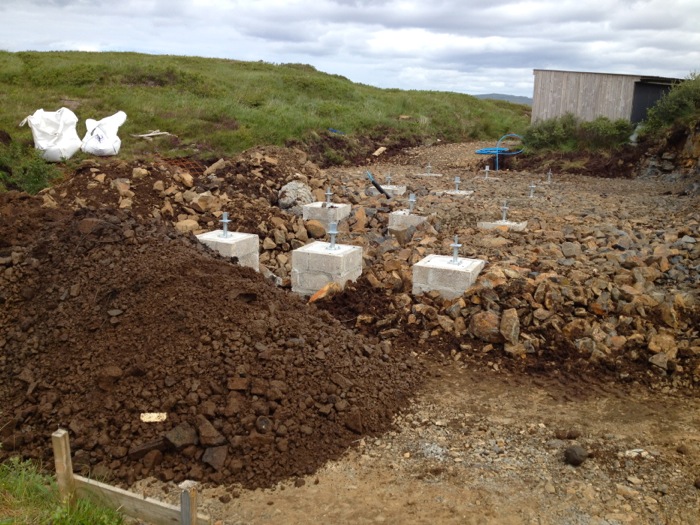
While he was back I put in the drainage to the soak away from the house and made sure the pop ups for water, electricity, and network connection were in the correct place inside the house.
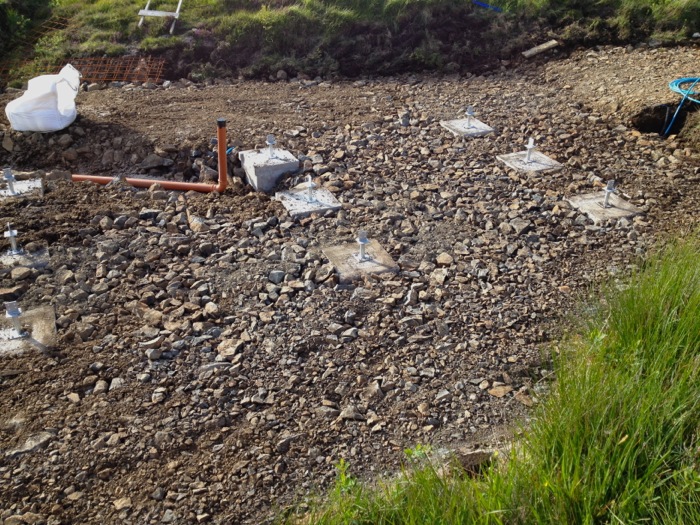
So all the work that we had so far done was out of sight. But we now had the base complete and were ready to begin on the wooden structure of the studio. Floor first.
Tags: Infill
02/07/15 21:08 Filed in:
Block Piers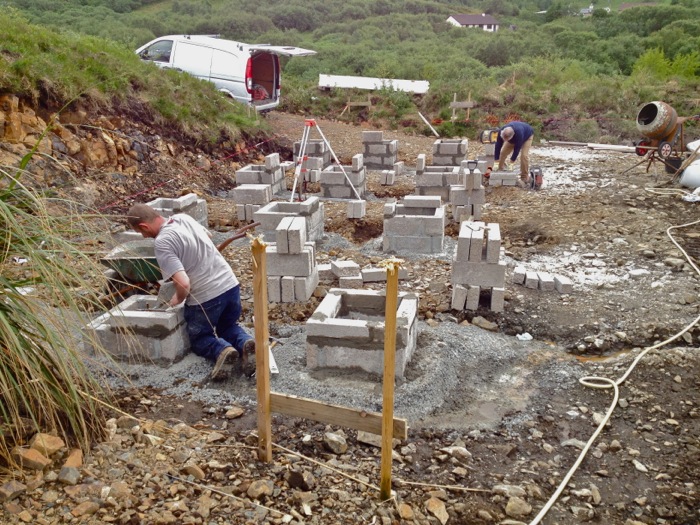
The job in front of us was building up the piers to the correct heights across the site. The piers were built up around the central reinforced cages once built to the correct height we had to mix concrete on site to fill each pier up level to the top blocks of each one.
We had a small petrol mixer on site and three bags of aggregate, sand and 20 bags of cement.
Simon did the blockwork while I mixed the cement for the mortar. Once the piers were built and had dried the task was then to mix concrete en masse to fill each of the piers up to the top. We worked together and swopped shovelling the mix into the mixer adding the water to get the correct consistency with wheelbarrowing it over to the piers to shovel in. Bloody hard work and I was knackered at the end of the day. It took a couple of days hard work to fill the piers.
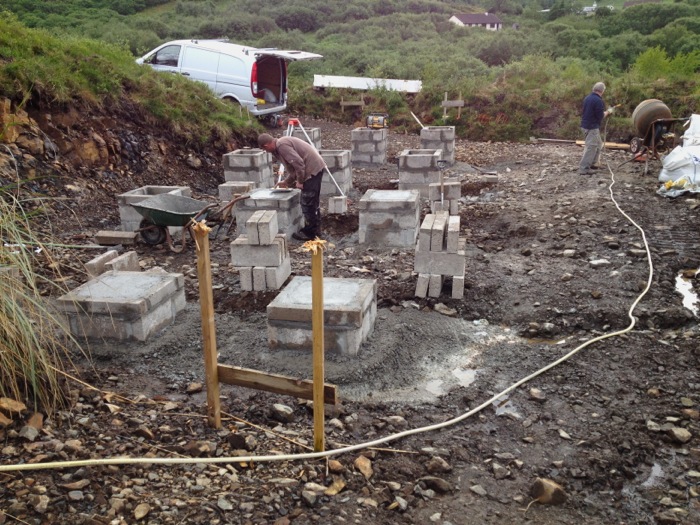
Tags: Piers